Production power at its best: flexibility and increased efficiency at Ebusco
Challenge
Flexible production with increased output
Production capacities need to be increased – but established structures and processes make this very difficult. What is more, customers’ requirements are becoming increasingly individualized, and need to be implemented flexibly. These are the challenges confronting manufacturing companies like Ebusco, a manufacturer of electric buses based in the Netherlands. The questions the company was asking were:
- How can production processes be adjusted to increase output?
- What can be done to guarantee future-oriented flexibility?
- Where might it make sense to switch to automation?
- What can be done to guarantee high quality?
Vision
Efficiency redefined. Production in the fast lane
Many companies need to rethink their production processes to be able to work as effectively as possible and save resources. Because the market is calling for rapid, flexible solutions. This also applies to Ebusco, a manufacturer of electric buses.
The specific aim was to significantly increase output while making production more flexible, safer and more modern. This is where EDAG came in. The details at a glance:
- Optimized worker utilization through multi-station principle
- Generation of increased output
- Systematic automation reduces the load on employees
- Adaptable tools to ensure that future customer requirements are met
Solution
Process optimization par excellence
A significant increase in output combined with flexible production for a wide variety of models: this is the result of a project carried out by EDAG for the Dutch electric bus manufacturer Ebusco. The successful aspects of the collaboration at a glance:
- Optimized automated production processes lead to a significant increase in output – doubling production capacity in body manufacturing
- Increased efficiency: Adapting the joining sequence processes and contents enables existing personnel to work more efficiently
- Automation where possible and appropriate: the employees’ workload is reduced, new solutions ensure improved working conditions
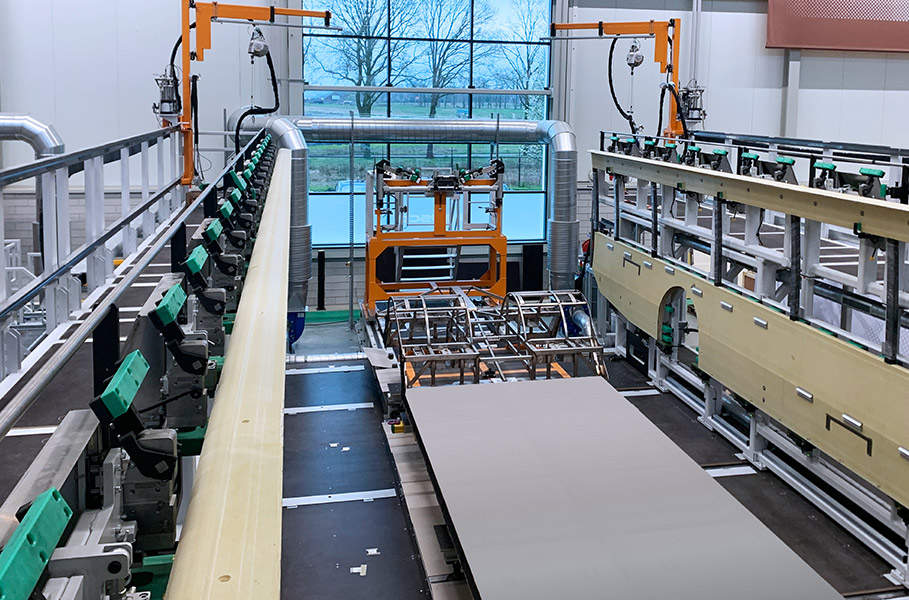
Challenge
Dynamic markets call for dynamic production
Intelligent process solutions designed to meet requirements
Customer requirements are changing, so companies will have to improve the efficiency of their production facilities if they are to survive on the market and still ensure excellent product quality. To keep up with this momentum, many manufacturing companies are having to rethink and improve their processes. Often, however, they lack an external point of view, the time or the requisite expertise: Where exactly do the processes need to be adjusted to future-proof them?
Automation and efficiency: output significantly increased
This is where EDAG PS comes in. With our high-level technical competence and process knowledge, we assist customers from a variety of different industries, and carry out an all-round examination of their processes. As we did for Ebusco, a Netherlands-based manufacturer of electric buses. The challenge was clear: production was to be taken to the next level, and processes improved in order to meet growing demands. In this project, EDAG PS supplied not only the design and engineering, but also the implemented the optimized production processes. Where appropriate and possible, EDAG PS also decided to automate processes that until then had been manual, in this way reducing the load on employees as far as possible and supporting them in their daily work.
The results at Ebusco:
- Reduction of operative personnel requirements in body manufacturing
- More homogeneous workflows
- A substantial increase in output
- Greater flexibility for product portfolio in production
- Modern working standards for employees
Vision
Engineering meets efficiency: EDAG PS revolutionizes production at Ebusco
Redefining quality and flexibility in bus production
EDAG PS supervised the Ebusco project from engineering to realization. The first step towards making the production line more efficient, increasing flexibility and further improving quality and working conditions for the employees was for EDAG PS and Ebusco to carry out a joint analysis of the status quo. While the individual production steps involved in manufacturing the electric buses were analyzed, the overall process itself also underwent a comprehensive review.
Twofold use, maximum efficiency: optimized joining sequence
EDAG PS conceived the process with the specific product in mind and, working on its own experience, recommended a different joining sequence. What do the details of the solution look like? EDAG PS designed a new joining sequence for assembling buses. A single joining station was converted into two, ending the linear process and making it possible to work in parallel.
In addition, a gripper was installed to automate a number of manual processes, for instance weighting glued parts with sandbags for the curing process. Power assisted and pneumatic technology is now used to move heavy loads. This reduces the load on employees, speeds up the process, and also helps to improve occupational health and safety.
Optimized production processes and the use of new, flexible tools also make for more flexible production. This allows, for example, the flexible and space-saving production of other bus lengths. As customer requirements are becoming increasingly individualized, Ebusco will be able to react quickly and flexibly to requirements and adaptations in the future.
EDAG PS:
- was involved in the entire project, from the concept idea through to construction
- was able, in an iterative process, to achieve the best possible results for Ebusco
- brought about a significant increase in output
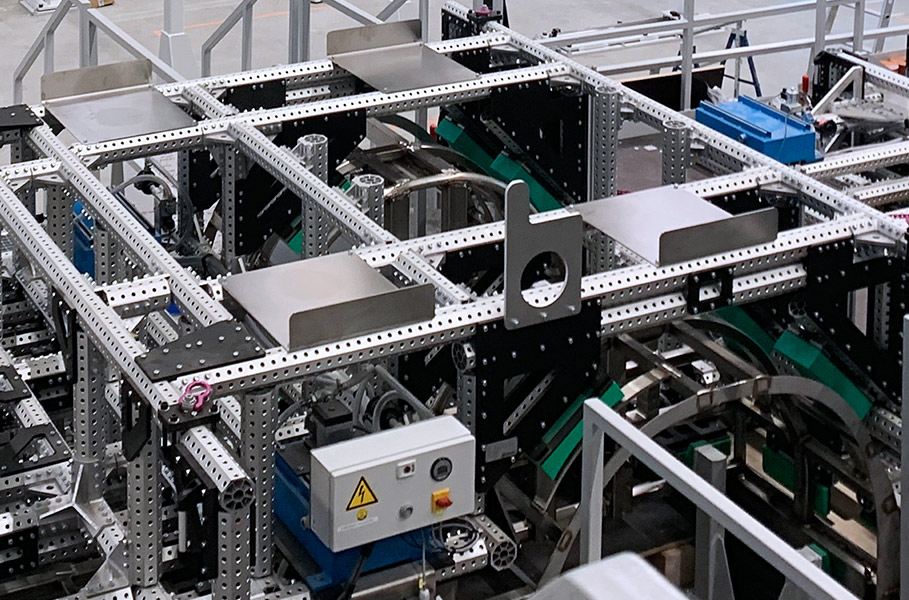
SOLUTION
From linear to agile: transformation of the production landscape
Efficiency in focus for modern bus production
Ebusco’s aim was to significantly increase production output and flexibility in the production of electric buses. EDAG PS saw the project through from A to Z: After a detailed analysis and conception phase, Ebusco benefited from EDAG PS’s sound process skills. By changing the production and joining sequence, it eventually proved possible to significantly increase output, and production capacities in body manufacturing were doubled.
Flexible production to meet individual customer requirements
In addition, automated processes and modern tools reduce the load on employees, saving time and increasing occupational health and safety. What is more, now that the entire production process has been examined and optimized, Ebusco can benefit from more flexible production.
In concrete terms, this means that new customer requirements can be implemented more quickly and easily, resulting in greater customer satisfaction and improved market penetration.
The facts at a glance:
- Different bus lengths can now easily be produced; individual customer requirements can quickly be implemented.
- Reducing the load on employees, new tools and the systematic automation of smaller process steps all lead to greater occupational health and safety.
- Perfectly coordinated work steps save time.
- Linear production was abandoned in favor of parallel work methods. Time that used to be spent waiting, e.g. for curing, can be put to flexible use